Industry professionals and DIY enthusiasts understand the crucial role that selecting the right fine wire screen plays in achieving the desired outcomes in various applications. Navigating through the myriad of options available, individuals often seek a solution that marries efficiency with durability. However, making an informed purchase requires more than just a basic understanding of product specifications.
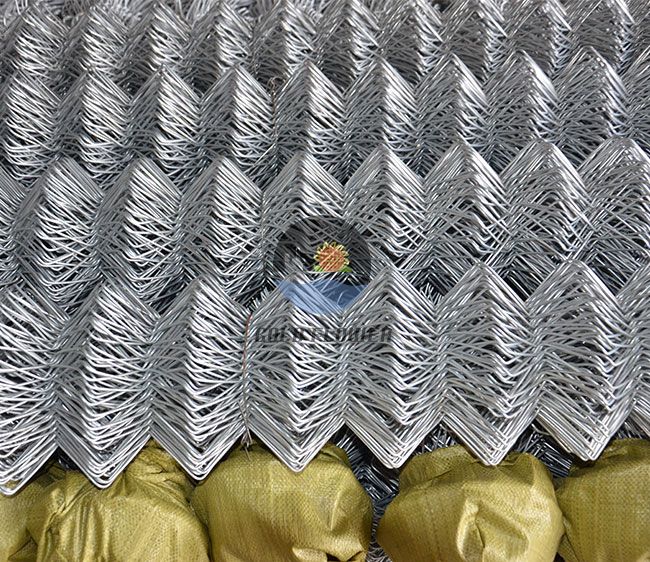
Fine wire screens are the unsung heroes in filtration, sieving, and separation processes, lending themselves to applications that span from industrial manufacturing to artisanal crafts. Their reliability in trapping impurities while allowing desired substances to pass through makes them indispensable. Yet, the true measure of a fine wire screen's value is its ability to maintain performance over time, resisting wear and corrosion.
When contemplating a purchase, expertise in the field suggests prioritizing the material composition of the wire screen. Stainless steel, for instance, is lauded for its corrosion resistance and strength, making it suitable for use in harsh environments. On the other hand, copper and aluminum offer flexibility and conductivity, catering to specific needs such as electronic applications.
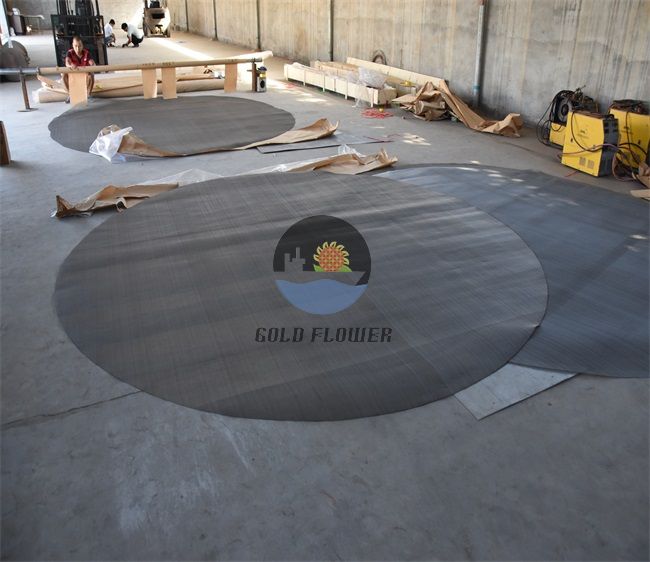
The configuration of the weave also demands attention. Expert insights highlight the advantage of plain weave for general purposes, balancing strength and permeability. In contrast, a twill weave offers greater flexibility and is often favored in applications requiring a tighter mesh. For those seeking specialized solutions, Dutch weave – characterized by its tightly woven weft wires and coarser warp – is optimal for high-pressure filtration systems.
Authoritative reviews consistently emphasize the importance of mesh count, which directly impacts the screen’s filtration ability. A higher mesh count facilitates finer filtration, ideal for capturing smaller particles, while lower mesh counts are sufficient for coarser processes. This expertise underscores the necessity of aligning mesh count with intended use, ensuring efficiency and precision.
buy fine wire screen
The debate between custom-made screens and off-the-shelf solutions persists among professionals. While custom screens promise precise specifications tailored to unique tasks, they often come with higher costs and extended lead times, challenging project deadlines. Conversely, standardized screens provide a ready-to-use solution, balancing cost and performance, a factor many small to medium-scale industries find appealing.
Warranties and certifications serve as indicators of trustworthiness in the product’s longevity and safety. Buyers are increasingly advised to prioritize screens sourced from reputable manufacturers who offer guarantees and comply with industry standards. This commitment to quality not only assures long-term reliability but also provides peace of mind, knowing the product is backed by a trusted entity.
The online marketplace has transformed how consumers procure fine wire screens, offering unparalleled access to a global selection. Nonetheless, navigating this digital landscape requires diligence; authoritative websites often recommend consulting detailed product datasheets and seeking peer reviews to gauge the satisfaction of previous users.
Case studies further illuminate the transformational impact of choosing the right wire screen. In the chemical manufacturing industry, for example, businesses have reported enhanced filtration efficiency and cost savings after investing in high-quality fine wire screens, evidencing the tangible benefits of informed purchasing.
Ultimately,
the procurement of fine wire screens goes beyond simple transactions. It embodies a strategic decision driven by thorough research, expert consultation, and a clear understanding of application-specific requirements. Empowered with these insights, purchasers can ensure that their selected wire screen not only meets but exceeds their operational expectations, reinforcing their trust in the quality and efficacy of their investment.