Wire mesh has long been an indispensable component across various industries, offering versatility and durability that few materials can match. As someone deeply engrossed in the nuances of this product, I've witnessed firsthand the transformative power it bestows on construction, manufacturing, and even art.
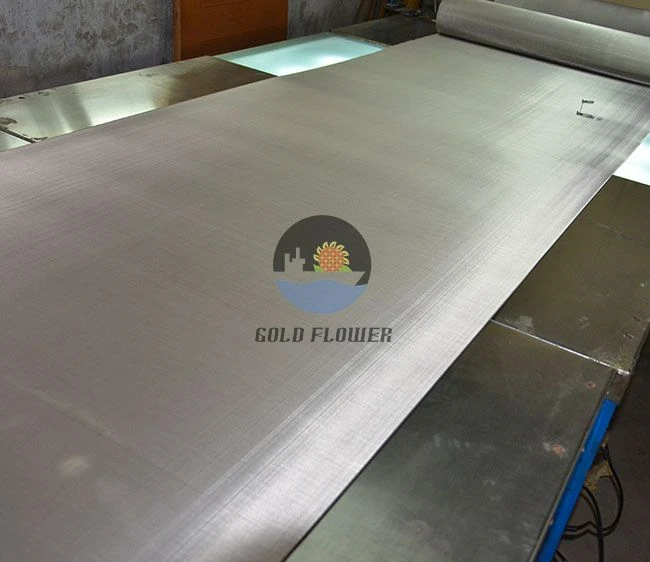
Drawing from years of experience in the field, wire mesh stands out due to its adaptability. Its ability to be customized to meet specific strength, flexibility, and size requirements makes it ideal for constructing barriers, reinforcing concrete, and even crafting artistic installations. This multifaceted application not only proves its economic viability but also enhances operational efficiencies across industrial operations.
The expertise required to choose the right wire mesh cannot be understated. Understanding the differences between welded and woven wire mesh, for instance, is crucial. Welded wire mesh offers a robust solution for heavy-duty applications, thanks to its strong grid structure produced through welding. This makes it an ideal choice for fencing and construction reinforcement. On the other hand, woven wire mesh, crafted by interlocking metal wires, offers flexibility and fine filtration capabilities, finding its niche in sifting and filtering applications.
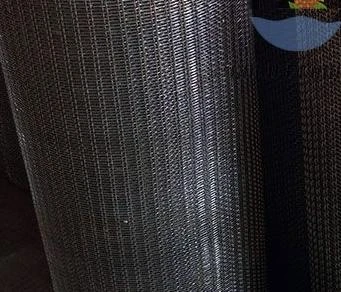
Engaging with industry experts has reinforced the importance of selecting the right material for wire mesh. Stainless steel is often favored for its resistance to rust and corrosion, making it suitable for outdoor and humid environments. Carbon steel, while less resistant to corrosion, offers higher strength and is cost-effective, thus preferred for indoor applications where moisture is not a primary concern. Galvanized wire mesh strikes a balance between cost-efficiency and durability, thanks to its protective zinc coating that offers moderate corrosion resistance.
The authority of wire mesh in safety applications cannot be overlooked. From securing perimeters with sturdy fencing solutions to ensuring the structural integrity of tunnels and bridges, it serves as an unseen backbone in safety architecture. Its role in these high-stakes environments underlines its reliability and engrains trust among engineers, construction experts, and safety officers globally.
wire mesh
Trustworthiness is further enhanced by adhering to quality standards. Renowned manufacturers adhere to international standards such as ISO 9044 for woven wire products or ASTM specifications for welded wire mesh. These benchmarks ensure that the wire mesh used across industries meets stringent quality and safety criteria, fostering confidence in its deployment for critical applications.
Innovative advancements continue to influence this industry. New techniques in coating technologies extend the lifespan of wire mesh products, while precision manufacturing processes have led to highly customized solutions catering to niche markets. The evolution of materials science and engineering continually refines the performance of wire mesh products, anticipating future needs and challenges industry faces.
Selecting the right wire mesh translates into leveraging a balance of strength, flexibility, and protection. It demands an understanding of the material properties, environmental considerations, and application demands. As transformations in this sector continue to unfold, they point towards an era where the wire mesh not only upholds its current applications but also pioneers new opportunities in the evolving landscape of modern engineering and design.
The enduring legacy of wire mesh in industrial and creative applications underscores its unparalleled versatility. With a commitment to quality and an eye on innovation, this unassuming product continues to shape our world in silent, yet significant ways, proving time and again to be an essential material in a multifaceted world.