Navigating the market for weld mesh can be a daunting task, especially given the diverse array of specifications, materials, and quality standards. Weld mesh, a versatile product used in construction, agriculture, and industrial applications, plays a critical role in structural integrity and overall project success. Here, we unravel key aspects that potential buyers should consider, leveraging deep industry insights to enhance your purchasing decision.
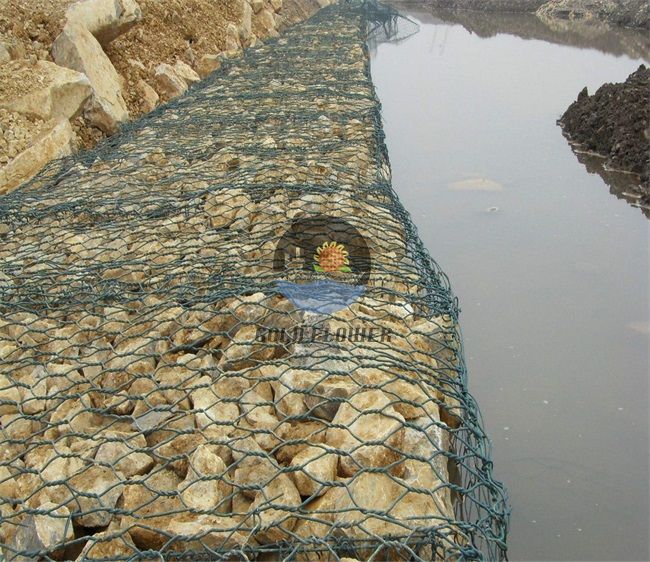
A cornerstone in any purchase decision is understanding the specific needs of your application. Weld mesh comes in various gauges, sizes,
and finishes. The wire diameter, also known as the gauge, determines the strength and flexibility of the mesh. Applications requiring heavy-duty support, such as fencing for livestock or secure enclosures, benefit from a thicker gauge. Conversely, thinner gauges are suitable for lighter applications like DIY projects or decorative features.
Material choice significantly impacts the durability and performance of weld mesh. Typically, steel or stainless steel options are prevalent, each offering distinct advantages. Standard steel mesh is cost-effective and widely used for temporary structures or indoor applications. However, when longevity and resistance to corrosion are critical, stainless steel is the superior option, particularly in environments exposed to moisture or chemicals.
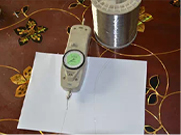
The manufacturing process and quality control mechanisms are vital indicators of product reliability. Reputable manufacturers employ automated welding techniques to ensure consistent weld quality and strength across the mesh. It's advisable to source from companies that comply with international quality standards, as this guarantees a level of performance that can be trusted over time.
Choosing the right mesh aperture is another crucial factor. Aperture size affects the visual and functional attributes of the mesh. For projects like animal enclosures, smaller apertures prevent escape while ensuring visibility and ventilation. On the other hand, construction applications may demand larger apertures to allow for concrete fill or support vegetation growth in landscaping projects.
buy weld mesh
It’s also important to consider the coating of the weld mesh. Galvanized coatings are common, providing a layer of protection against rust and wear. When selecting galvanized mesh, a higher zinc coating weight results in better corrosion resistance and extended lifespan. For projects in highly corrosive environments, opting for PVC coated mesh provides additional protection, alongside color customization to blend or highlight structural elements.
Supply chain reliability is a key consideration. Engaging with suppliers who offer transparency in their sourcing and logistics processes can mitigate risks associated with delays or quality discrepancies. Suppliers should provide clear information on lead times, shipment tracking, and post-purchase support, ensuring a smooth transaction from order to delivery.
Finally, the price-to-value ratio cannot be overlooked. While budget constraints are a reality, focusing solely on cost can be detrimental to project outcomes. Evaluating the total cost of ownership—which includes durability, maintenance, and potential replacement—often reveals that investing in higher-quality mesh offers better long-term value.
In summary, buying weld mesh involves a comprehensive evaluation approach that balances technical specifications with practical implications. By focusing on material quality, manufacturing integrity, application-specific attributes, and reliable supplier practices, buyers are better equipped to make informed decisions that enhance project success and durability. Whether for construction giants or small-scale artisans, these insights serve as a foundation for superior mesh procurement, reinforcing project excellence and safety across industries.